New research sheds light on how manufacturing choices influence microfibre release in textiles
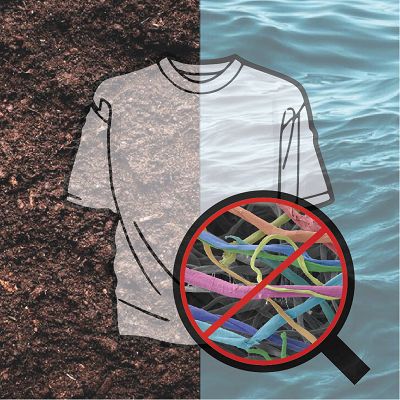
New research sheds light on how manufacturing choices influence microfibre release in textiles
Changes to fibre composition and the systems used to spin yarn could reduce the release of microfibres from textiles and their harmful impacts on the environment, new research from the Faculty of Arts, Humanities and Cultures’ School of Design has found.
Washing synthetic fabrics can release millions of microfibers, which harm the environment – particularly marine life – and can take hundreds of years to degrade.
Using a washing simulator (gyrowash), a research team led by Alice Hazlehurst, doctoral researcher in the School of Design at the University of Leeds, tested various densities of yarns in unknitted hanks and knitted forms, and compared how much microfibre they released when washed.
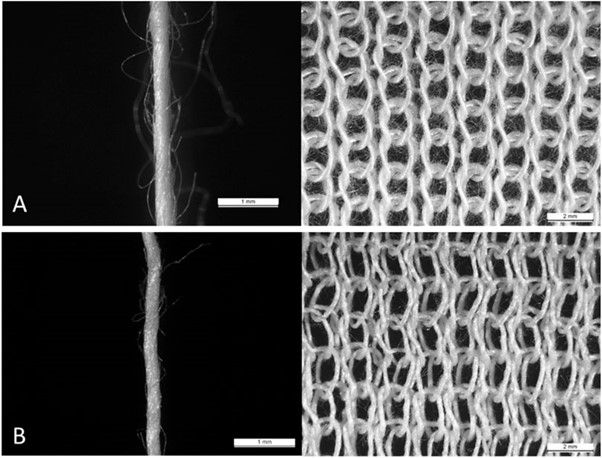
Comparison of yarn hairiness for yarns of the same linear density (30 tex) and different spinning systems. Source: ‘Investigating the influence of yarn characteristics on microfibre release from knitted fabrics during laundering'.
The researchers found that:
-
Unknitted polyester released more microfibre than unknitted cotton, but similar amounts were released when polyester was knitted. This suggests that polyester suffered less damage than cotton during the knitting process
-
Microfibre release in tightly knitted fabrics during laundering was reduced, but manufacturers should considered fibre fly – the visible ‘fluff’ that comes off fabrics as they are knitted in factories – which is higher when garments are tightly knitted
-
Vortext-sun yarns (where fibres are twisted using jets of air in a vortex) had a lower microfibre release than ring-spun yarns (where fibres are twisted in a metal ring). Ring-spun yarns tend to be ‘hairier’ than vortex-spun yarns, which has been shown to increase microfibre release in washing.
The researchers concluded that changes to the fibre composition and the yarn spinning system would have the greatest influence in terms of reducing microfibre release. However, these details are not currently included in product specifications, which makes it more difficult for brands to make informed choices about which garments will release more or less microfibre.
Our findings show that the entire process of textile production, down to the way yarn is spun, is important in the effort to limit microfibre release. Manufacturers should contain these details in specifications of yarn spinning, as well as the fibre type, to help clothing designers make more informed choices.
More research needed
The academics are also calling for more research into the effects of microfibre release on the environment and human health so measures can be targeted towards reducing harm.
We know cotton produces more microfibre than polyester and people assume that cellulose (from cotton) is less worrying than microplastic because it’s natural. But the truth is that we don’t have enough information about the impacts of these fibres on humans, aside from knowing they can take hundreds of years to biodegrade and can have a negative impact on marine life.
Dr Mark Sumner, Lecturer in Sustainable Fashion at the School of Design, added: “Our previous research found that UK washing is a huge source of pollution, releasing an estimated 1,500 double decker buses worth of microfibre every year, so it’s important that information about fabric knitting and yarn spinning systems are included in specifications.”
‘Investigating the influence of yarn characteristics on microfibre release from knitted fabrics during laundering' by Alice Hazlehurst, Dr Mark Sumner and Dr Mark Taylor (all from the School of Design, University of Leeds) was published in Frontiers in Environmental Science. The research was funded by The Microfibre Consortium (TMC) and has been covered by Ecotextile News.